INTRODUCTION
You shouldn't compromise air quality on a job site. When heating, air conditioning, or ventilation is needed, you have to be able to bank on a duct to deliver fresh, heated, or cool air into the space your crew or occupants are working in.
The fabric of a portable duct serves as the skin, designed with each duct's unique purpose. Any manufacturer worth their salt will be able to strip down their ducts and show how, piece by piece, they're built for quality and a specific purpose.
When it comes to the types of duct fabrics available, what makes them different?
How different can they even be? It seems simple enough, but sometimes, specific situations call for particular fabric requirements and the coatings applied to them.
** This article is provided for informational purposes only.
In This Guide, You'll Learn:
Duct Fabrics: The Best Materials
Distributing air on construction or industrial sites can be crucial as we’ve discussed. The portable ducts you use are conduits for the air pumped from permanent or portable HVAC systems and serve as the de facto lungs of a building or structure.
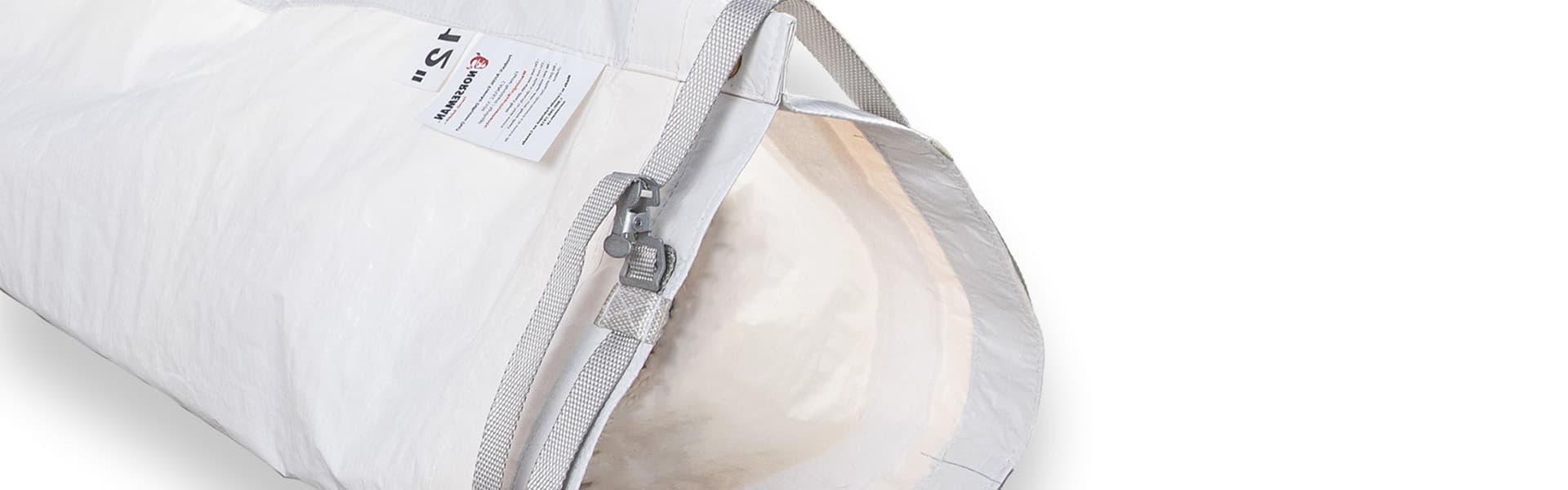
AC & Ventilation
Air quality is something we know is crucial to your workers or occupants as air quality. In the case of most cooling or ventilation ducts, utilizing a material that won't badly puncture or tear to allow air to escape is an important component of maintaining air efficiency.
However, equally essential would be fabric that won’t have moisture accruing or saturating the duct, which can contaminate the air being transported inside with mold, mildew or other pathogens into the work space.
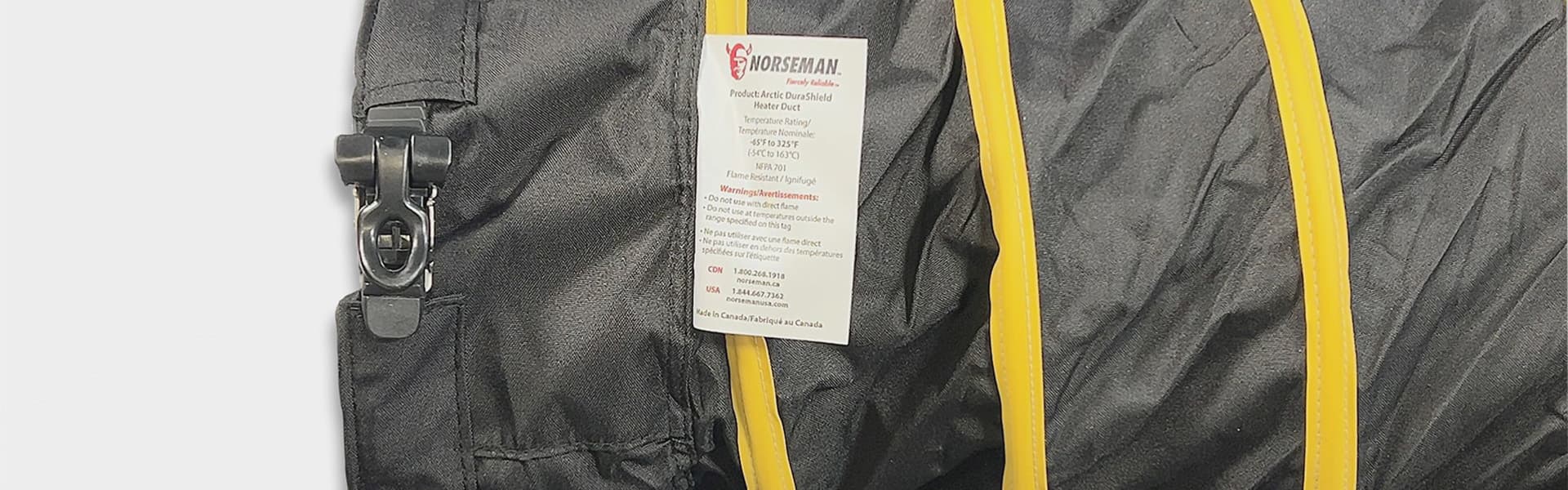
Heating
Industrial HVAC units can pump out some serious BTUs and as a result, the unit can get quite hot. You want to make sure that the duct being attached to one of these units will handle the intense heat output.
Smoke carrying chemicals used in the fabric or coating, or other toxic inhalants caused by a duct burning beyond its heat capabilities is a sure way to compromise air quality (and also send the fire trucks racing to your job site). Therefore, you want to use a material that’s rated to handle high temperatures or have a coating that’ll prevent the fabric from smoking or burning when faced with the high temperatures of the unit.
Duct manufacturers must be conscious of all the hazards from ducts that fail to meet air quality standards. They start by selecting the best materials, fabrics, and coatings to make efficient ducts for all applications.
Fabric Type Examples
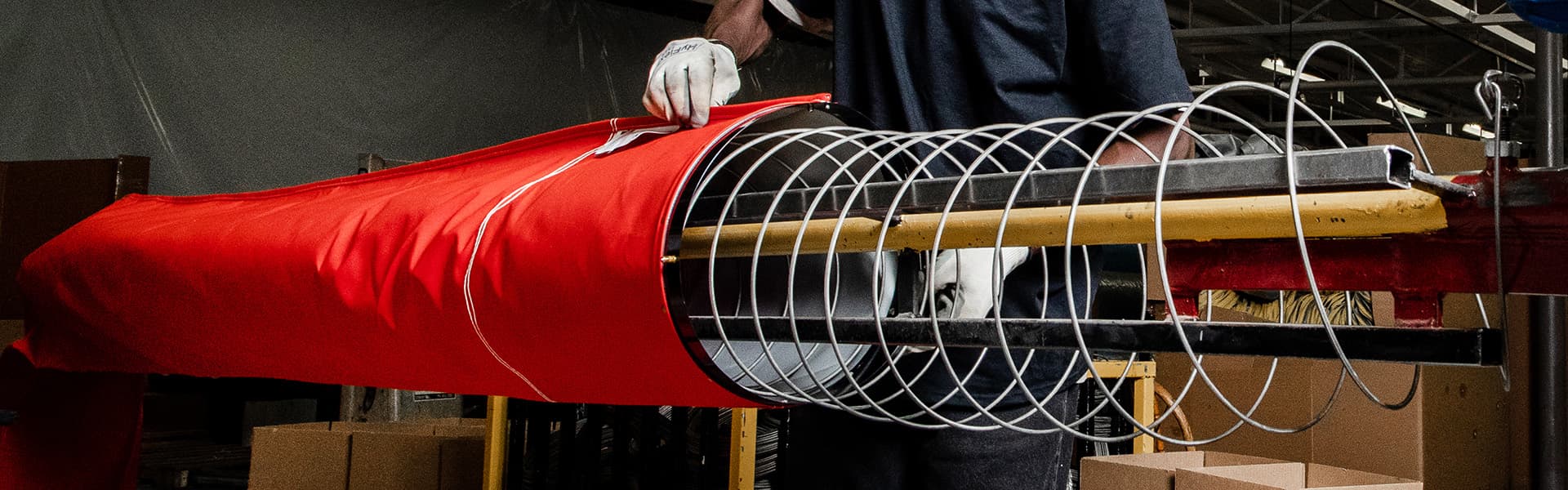
Polyester Fabric
Polyester is a synthetic fabric usually derived from petroleum. It's one of the world's most popular textiles and is used in many portable temporary ducts for its low cost, flexibility, and resistance to shrinking or swelling.
Polyester is the material used in many temporary ducts. It's strong enough to resist the rigors of construction and industrial sites as well as exposure to many different chemicals.
However, stain removal can be an issue because polyester absorbs slower than other materials. However, coatings can be applied to the fabric to counteract deficiencies, such as stains, moisture/mildew buildup and fading caused by UV rays.
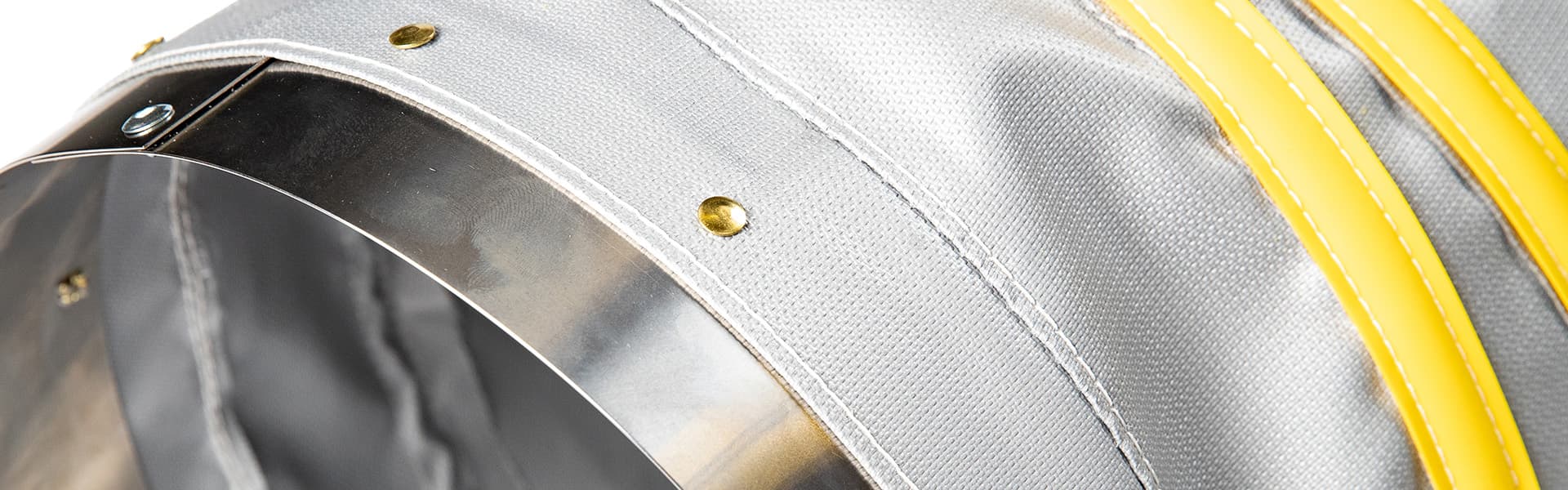
Fiberglass Fabric
Fiberglass is another excellent fabric for portable ducting. One of its chief advantages is that it can dampen or reduce HVAC machine noise when running. This makes it a popular option for offices or other commercial building ducts. Fiberglass fabrics are well-insulated and can also be coated to combat other elements like UV rays or mold growth.
Fiberglass ducts also typically have suitable linings that fight heat loss, making them ideal for heating duct applications in colder climates. The fabric is engineered to be lightweight without sacrificing strength, making it easier to install while holding up well against abrasive surfaces.
The installation of fiberglass ducting, in combination with an efficient heater unit, can significantly improve air quality and temperature in a desired space.
Thermoplastic (Rubber Ducts)
Rubber ducts are made from thermoplastic elastomers (TPE), which can also be called thermoplastic rubber (TPR) ducts. TPE rubber is made from a mixture of different polymers, such as plastic and rubber.
Thermoplastics are more challenging to manufacture when compared to other fabrics like fiberglass or polyethylene and typically need to be created through injection molding. TPR ducts have the ability to stretch to fit a specific situation with the ability to return to its near-original shape, making it an adaptable material option.
Thermoplastic rubber ducts are usually designed for general purposes and might not be ideal for a heavy-duty job site. However, their ability and efficiency are worth mentioning for ventilation applications to the average homeowner. A construction or industrial company needing portable ducts for heating or cooling should seek a material better suited for use against abrasive materials and connection to industrial HVAC units.
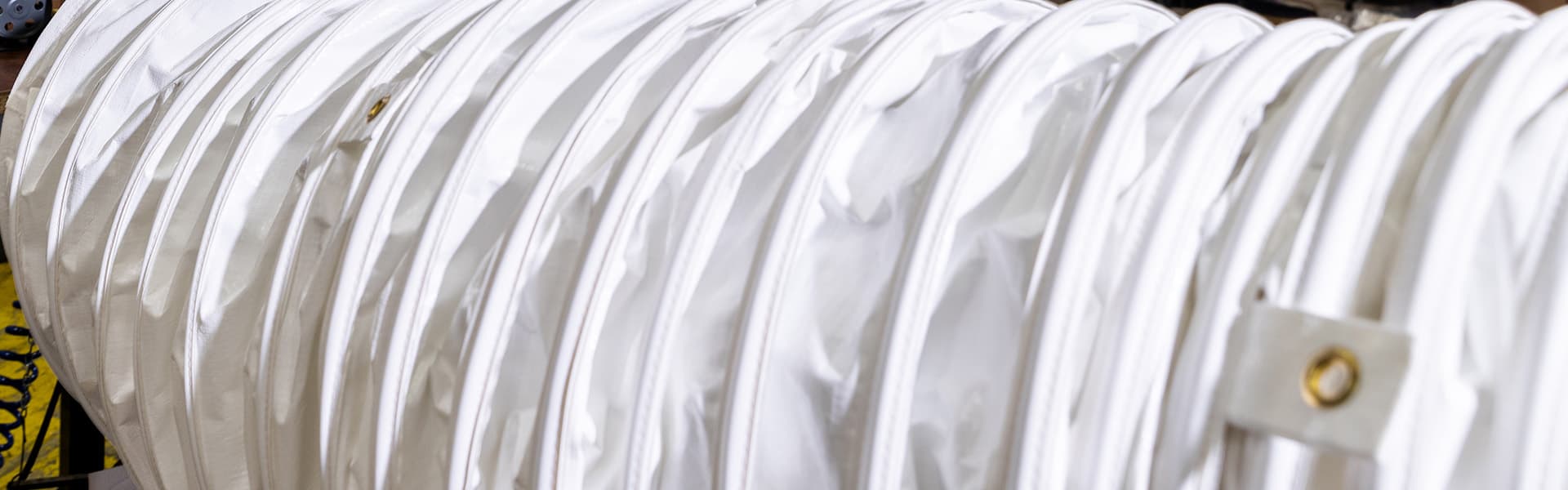
Polyethylene Ducts
Polyethylene (PE) fabric is a lighter fabric consisting of a woven scrim material protected between two outer layers of plasticized coating. These coatings contain helpful additives that contribute to the long-lasting nature of PE portable ducts.
PE coatings can also provide different benefits depending on the job requirement. A fungicide-resistant coating, for instance, will resist mold growth if a duct is used in an environment with high humidity or precipitation. Conversely, ultraviolet stabilizers may be added to the fabric to prevent fading or discoloration under the sun's intense rays. Flame-retardant coatings are also typically available.
Before PE fabric, the tension of existing fabric membranes posed a significant problem for manufacturers and installers. Polyethylene fabric, however, performs better when the material is subjected to proper tension both horizontally and vertically. Therefore, manufacturers realized that PE fabric attached to a duct's helix coil structure ensures minimal movement under pressure from the various environmental loads.
Polyethylene fabric is incredibly versatile. It offers total design flexibility, and the duct can serve many diverse applications across industries. The various use cases include construction projects, remediation jobs, HVAC uses in rental spaces, athletic facilities, indoor riding arenas, entertainment centers, and more.
Fabric Coatings
Manufacturers are constantly looking for ways to get an edge with their fabrics. One of the best ways to enhance a fabric used for industrial purposes is to use a coating to give it a new benefit it previously didn't possess or to improve its natural ability to wick away moisture, resist flame or UV rays and resist any other potential workplace hazard.
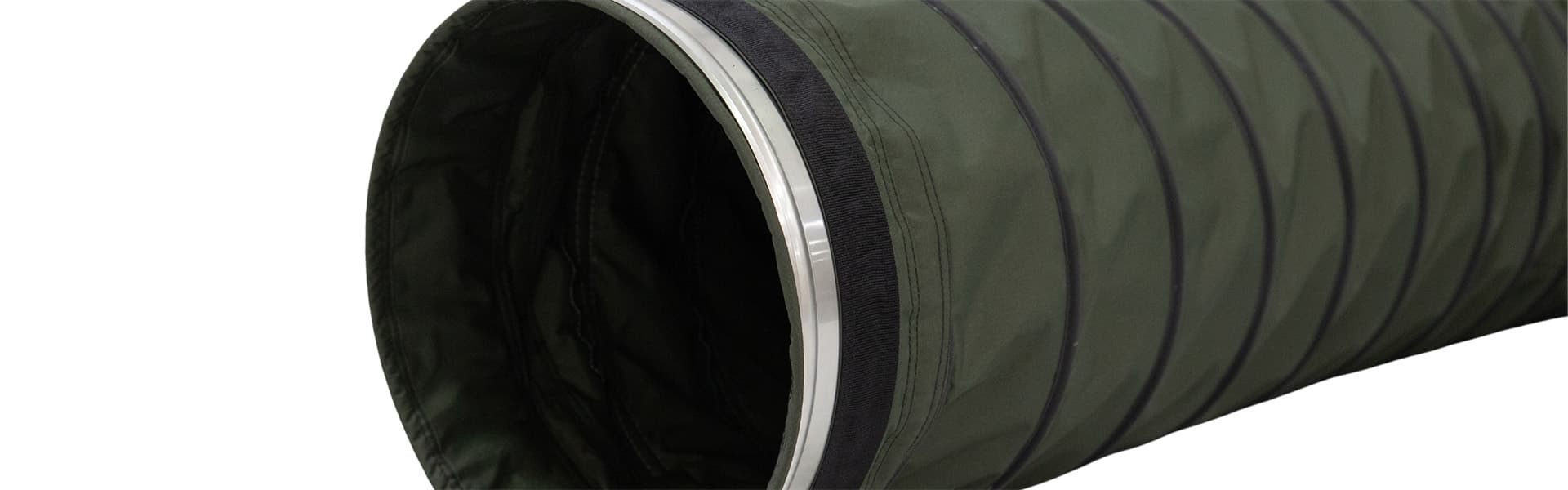
Pump Up the Polymer
Most coatings are created from synthetic polymers. A polymer is a class of substances composed of large molecules called "macromolecules," and multiples of simpler chemical units called "monomers."
Great, but what does that mean in plain English?
A polymer is basically a complex compound of molecules that chain together to form many different substances. ‘Synthetic polymers’ are man-made combinations that include plastics, rubber, and even Teflon.
Polymer coatings, in particular, offer enhanced protection on the surface of textile products while still allowing for water evaporation through the fabric—a process that is often hindered by other coating materials.
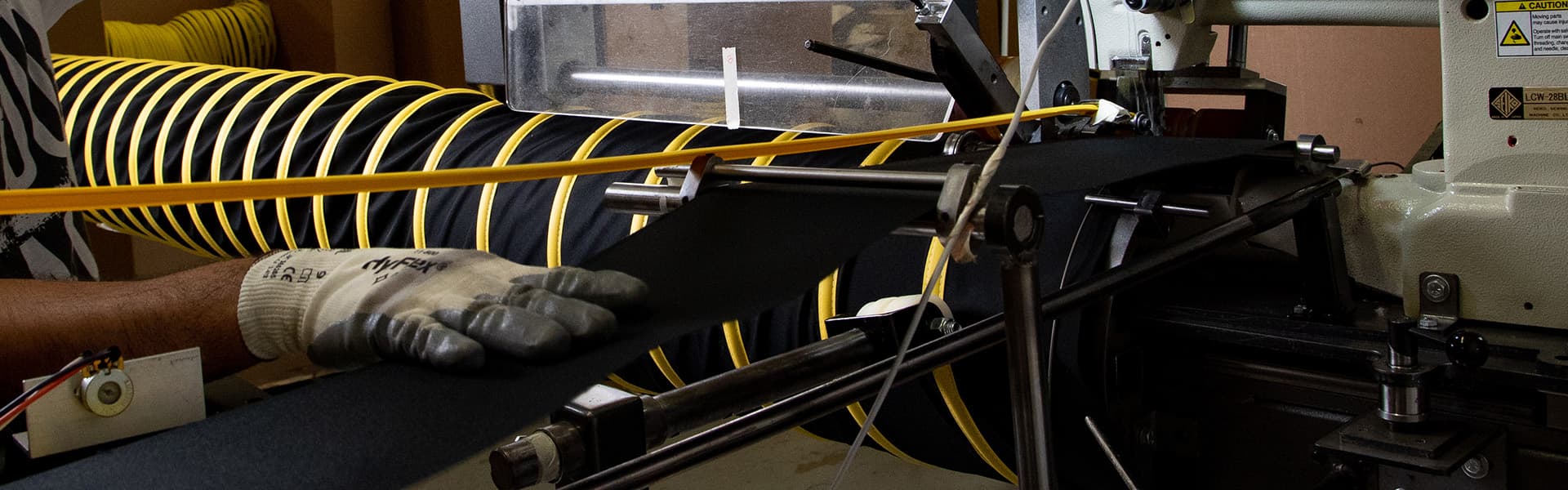
Urethane Coating
Urethane is a crystalline compound that has been heated with alcohol and an acid catalyst. The resulting polymer looks like a white powder but can also be in liquid form. The type we'll be looking at is liquid urethane, which is used on portable duct fabrics.
Liquid urethane is used as a coating, adhesive, or sealant. It can be found in pesticides or fungicides and also as a way to treat duct fabrics. Products coated with urethane are typically water, stain, and soil-resistant. This is valuable for portable ducting as it helps repel moisture buildup and keeps the duct clean and spotless for extended life.
Fabrics with a urethane coating are also responsive to radio frequency (RF) welding processes, which fuse duct seams. The RF welding process forms airtight and watertight seams for two or more surfaces, while the urethane coating helps improve the durability and functionality of the end product.
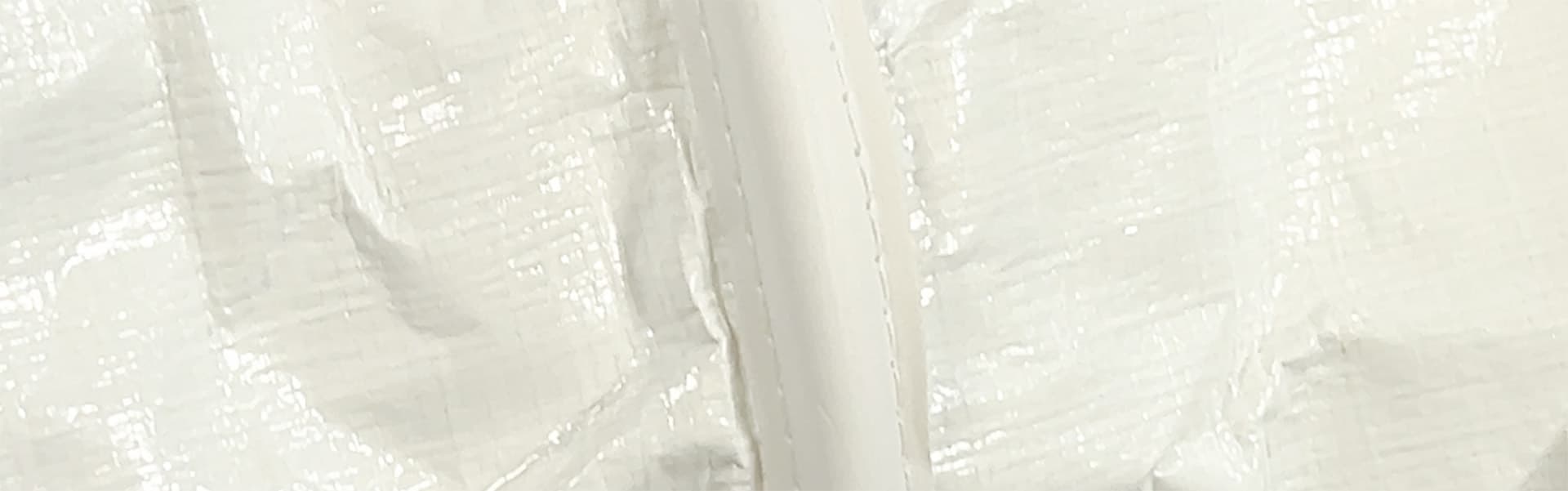
PVC-Coated Fabrics
PVC, or polyvinyl chloride, is one of the most widely produced polymers in the world. Some estimates say that 40 million tons are produced every year. You may know rigid PVC for construction pipes, doors, and windows, but it can also be used as a coating on duct fabrics.
PVC coatings help make the coated fabric waterproof, resist dirt, and give the duct material added strength and durability. This added benefit of strength is because the PVC coating on fabric helps prevent it from fraying, ripping, or tearing easily. This is an added plus when the duct in question is being used for heavy-duty purposes.
When combined with polyester, PVC coatings give the fabric excellent tensile strength while often including fire retardant additives, anti-fungal, and UV stabilizers to bolster the resistance of the duct fabric. This can be done for a lesser cost and provide an economical duct solution that won't skimp on the protective properties as an affordable alternative.
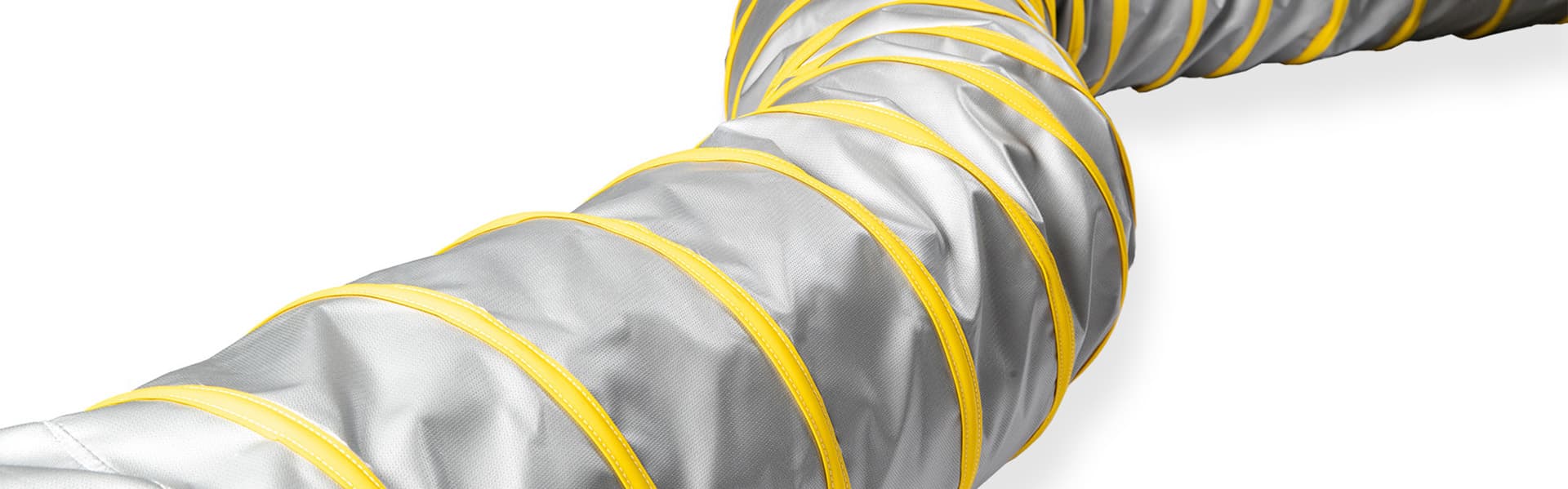
8 Examples of Polymer Coatings Features
Here are the ten primary benefits of polymer textile coatings:
Abrasion Resistance: Abrasion resistance is measured by rubbing flat, often coarse, materials against the duct fabric to see if there's any erosion, tearing, or deterioration of the fabric. Polymer coatings designed to resist abrasion create a layer on top of the textile fabric to increase abrasion resistance and protect the fabric weave.
Adhesives: Duct fabrics can be coated with specific polymers that increase their adhesion and tack to other surfaces or even other polymers if desired for specific jobs.
Air-Holding Capabilities: Polymer-coated textiles can incorporate resistance benefits to stop items like air or water from passing through the fabric. This makes them particularly useful in portable ducts where minimizing air loss in the duct network is crucial for efficiency.
Antimicrobial Properties: Some synthetic and natural polymers have been found to display antibacterial activity, sometimes even terminating up to 99% of bacteria it comes in contact with. These are useful in many different medical appliances and prevent mold and other harmful bacteria growing on the duct’s surface.
Flame Resistance: This is arguably one of the most common features required for heat ducting to resist the high BTUs of industrial HVAC units. Particularly where the duct connects to the unit. Flame-resistant agents like polyimides or polybenzoxazoles (PBOs) commonly create a highly flame-resistant coating that helps prevent a material from catching fire, smoking or smoldering when exposed to high unit temperatures.
Durability: Polymer coatings make textiles more sturdy and corrosion-resistant, significantly extending the service life of portable ducts and keeping them looking new.
Waterproofing: Polymer coatings provide an excellent means for waterproofing textiles. The hydrophobic nature of these coatings ensure that materials coated in particular polymer blends easily repel water and other liquids, keeping duct materials dry and prevent oversaturation. This is valuable in remediation work for AC and ventilation ducting.
Weldability: Some polymer coatings may need to be bonded through adhesives or hot air welds. These types of duct fabrics are ideal where a durable sealed seam is required. Customarily, sewn seams can create unwanted burn holes in the duct fabric, so this weldable bonding keeps the material intact.
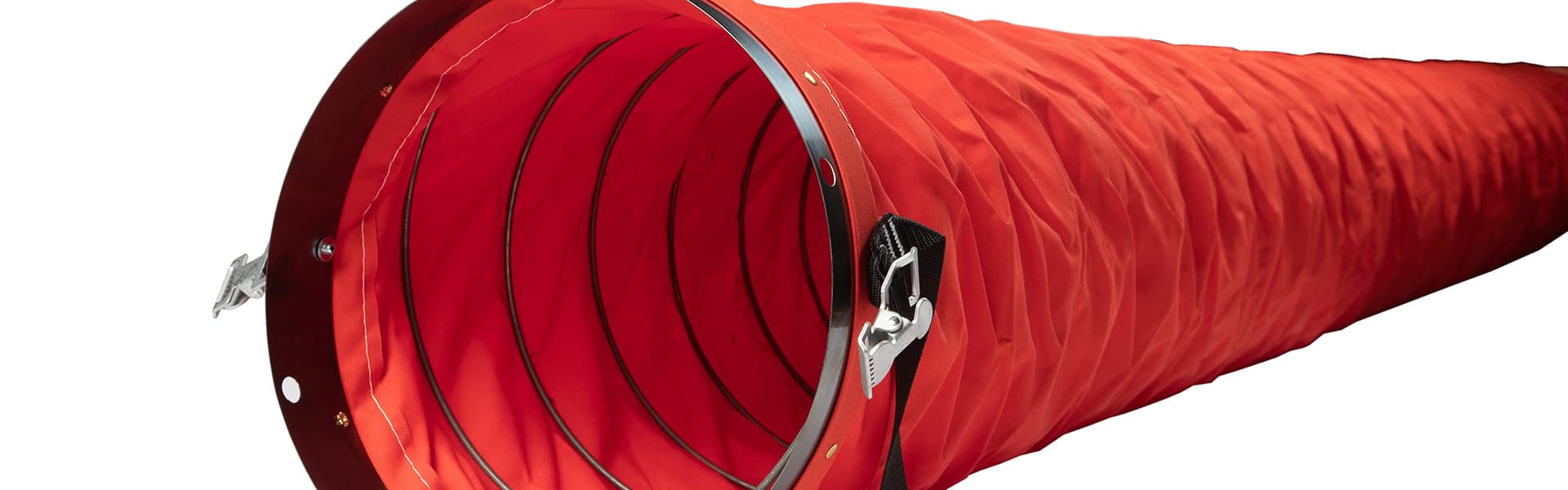
Let's Look at Polyethylene Coatings
Polyethylene (PE) coatings are among the most widely used coatings for fabric ducts. This is because they provide overall strength, durability, and resistance to mold, mildew, and UV damage.
A polyethylene coating on heat ducts can resist sub-zero temperatures that would otherwise freeze and crack the duct. The polymer helps keep the fabric flexible and perform optimally in winter.
Similarly, a PE coating on an air conditioning or AC duct helps prevent moisture from building on the duct material, preventing mold and mildew growth. No matter the purpose of the duct, the PE coating aids in its performance.
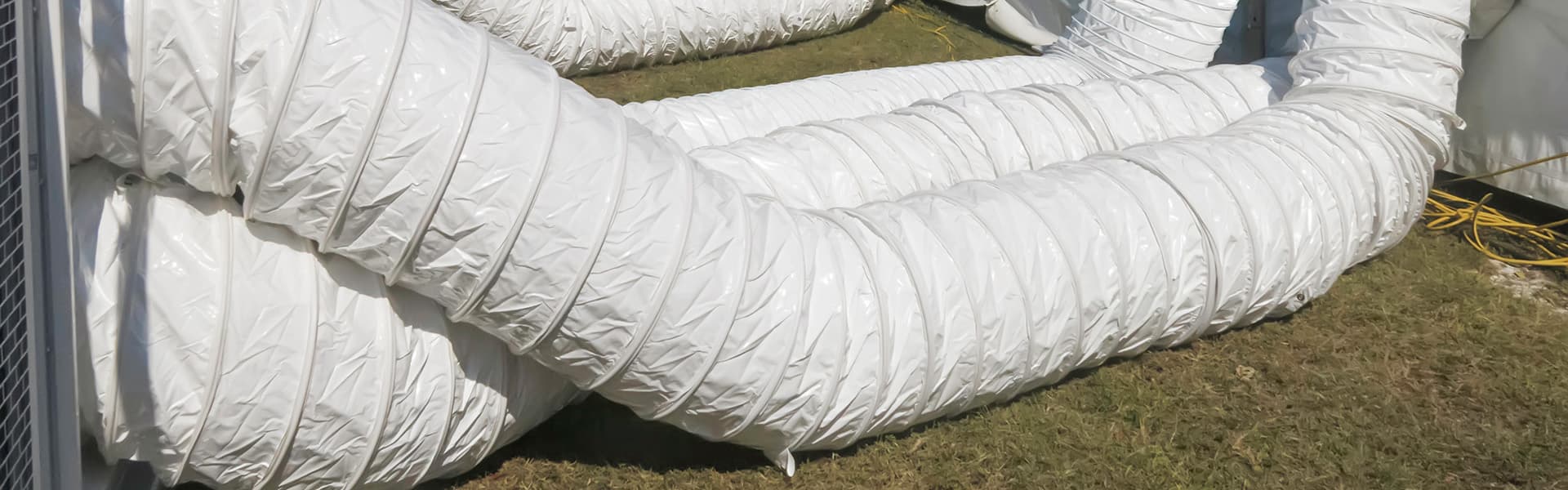
A Few Notes on Duct Structure
It's essential to take into consideration the structure of a duct's fabric on the skeleton of the duct structure. Most portable ducts use a metal wire coil as the structure that serves as the skeleton of the duct.
Therefore, it's very important that the duct fabric can adhere to and articulate with the duct's movements to maintain structural integrity and prevent tearing from the metal coils.
One manufacturing method that achieves this is sewing the fabric onto the coil structure. This helps prevent the duct fabric from "caving" in on itself and maintains the cylindrical helix tube pathway regardless of the presence of any airflow.
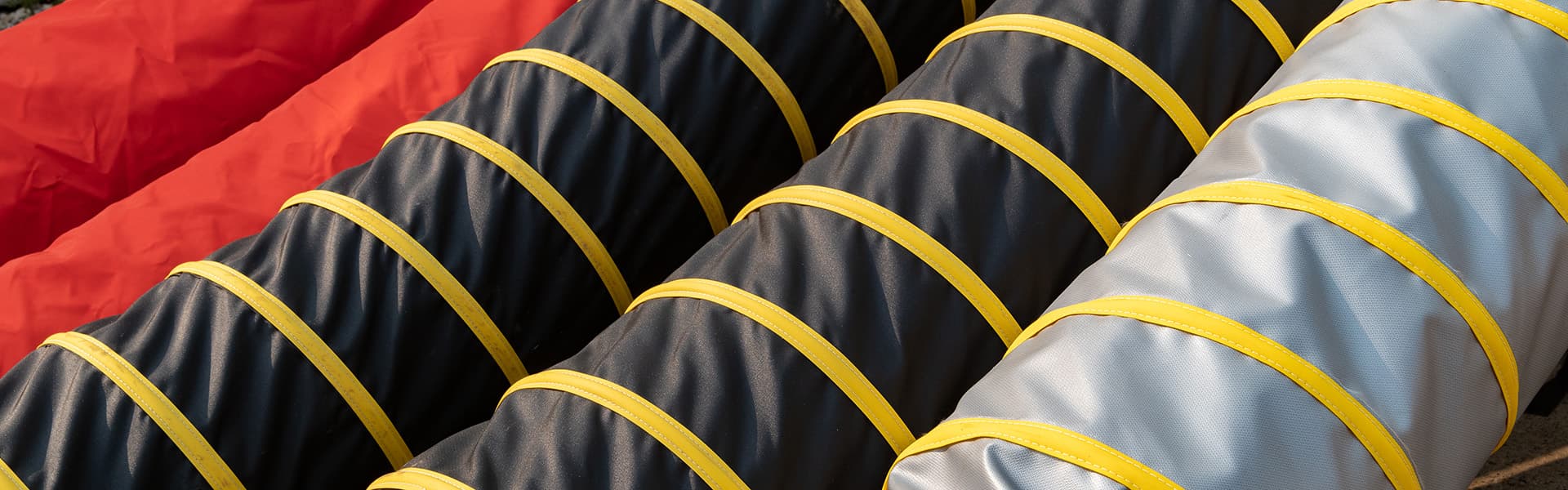
Conclusion: The Best Materials
Portable fabric ducts are an excellent vehicle for delivering air into a designated space, and the premium duct fabric options available help bolster their effectiveness. It’s obvious that using the best materials will ultimately produce the best results for your intended application.
Coupled with the polymer coatings on the duct fabric, there's essentially a combination of fabric or coating that will be suited for any sort of application.
All of this goes into the overarching theme of air quality within portable HVAC applications. This dive into fabric and coatings illustrates that portable ducts, whether used for heating, cooling, or space ventilation, can be engineered to maximize benefit for the desired situation.
That is how you truly create gear to perform!