Introduction
When we delve into the realm of foam fabrication, we enter a world with unlimited possibilities. Modern manufacturing technology, prototyping, and vast material selection give wings to almost any project idea.
This logic couldn’t be more applicable in terms of custom case inserts. Cases are used with all manner of equipment, tools or technology to pack around safely and efficiently. But with so many options available, how do you narrow it down to precisely what you need?
This article will help decipher those questions. It’s time to dive in and break apart this process so you can easily navigate the seas of foam fabrication.
** This article is provided for informational purposes only.
IN THIS ARTICLE YOU WILL LEARN...
What’s a custom case insert?
A custom case insert is a manufactured foam unit that fits within the confines of a container or case and protects fragile or expensive equipment or components stored during transport or storage.
We’ve all seen action movies where an intense, shady deal is going down in a dilapidated warehouse and one crime boss beckons for the henchman to bring up the briefcase full of money.
It usually has a sleek design and crisp clicking sounds as the buckles are unclasped. Then the lid is finally flipped open and you see the cash inside.
The money is attractive, but that goes without saying. However, have you ever paid attention to the case it’s carried in? How about the inside detailing of that case that perfectly encases the crisply packed dollar bills in acute professionalism? These unsung heroes are the custom case inserts.
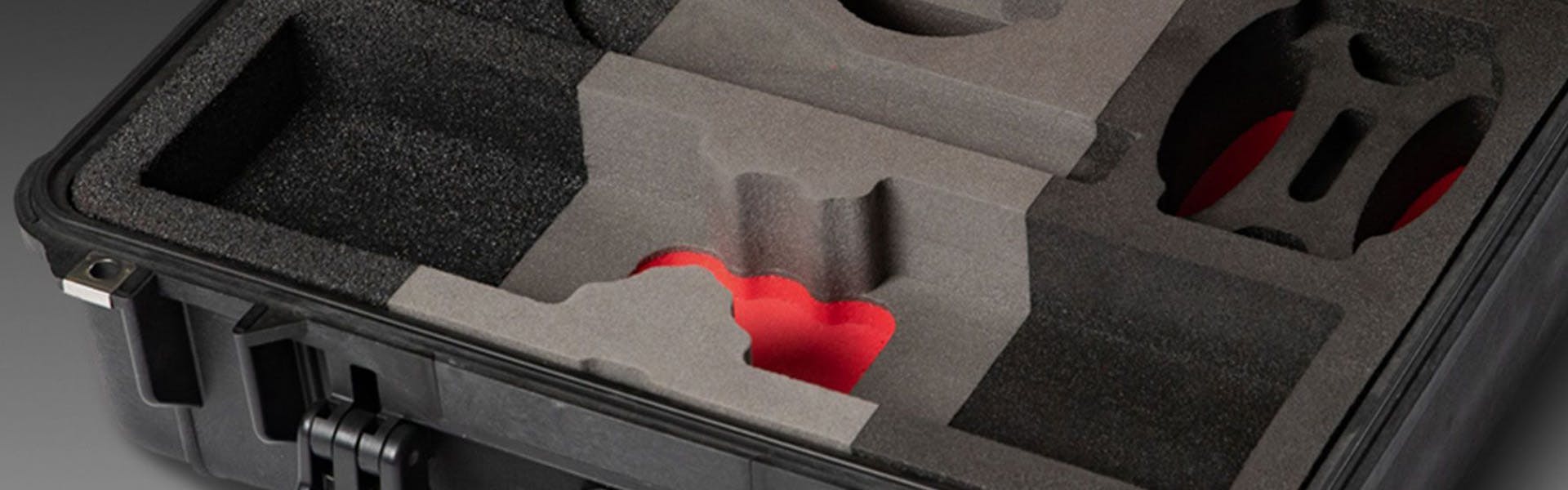
Why would I need a custom case insert?
We can all appreciate a good case. They’re protective and convenient as they carry all manner of essential equipment. Audio/visual equipment, cameras, drones, scientific and musical instruments, tools and even weapons can be transported in them.
However, all these examples come in different shapes and sizes and only some cases will fit all. This is the beauty of custom case inserts, though. There is no cookie-cutter approach and the customization of said insert is the specialty advantage that manufacturing one has.
Choose from the foam type, design specs, and color you wish to use. A well-designed custom case insert isn’t a luxury but a smart investment.
So, let’s look at how we would begin a custom case insert project.
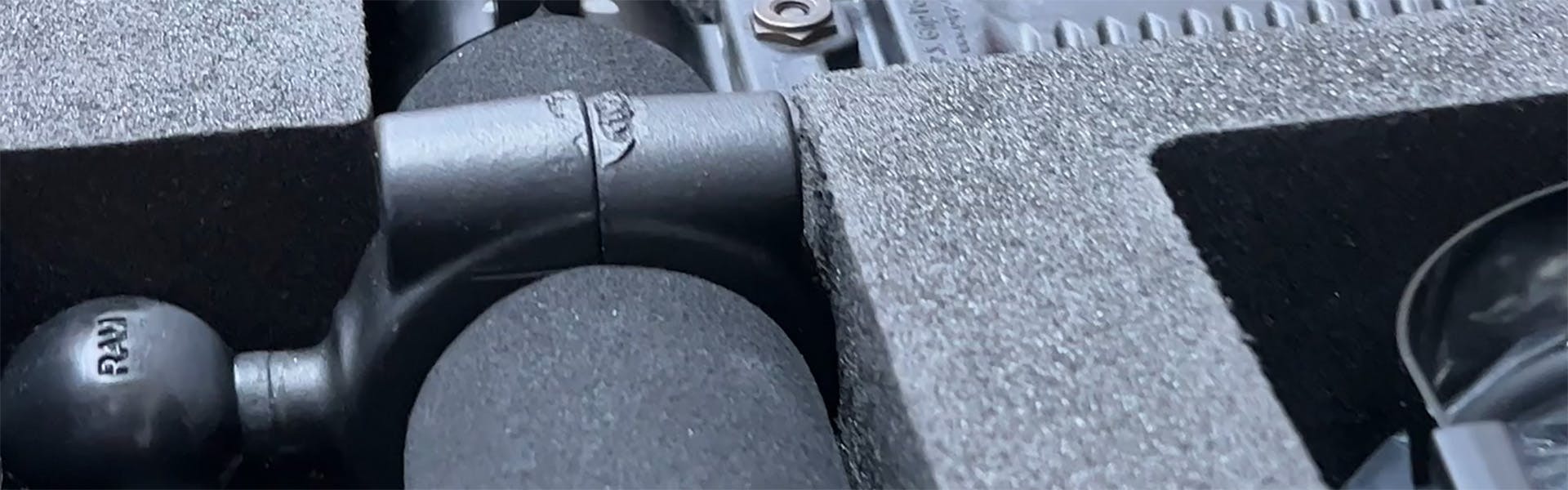
How To Begin Your Custom Case Design
We’ve established that custom case inserts are tailored to your specific requirements. The carrying cases themselves can be plastic, metal, or even fabric.
Suppose you think there’s diversity in the carrying case’s shell material. In that case, it has nothing on how much you can compare foam densities, rigidity, color or any other unique properties for the case insert.
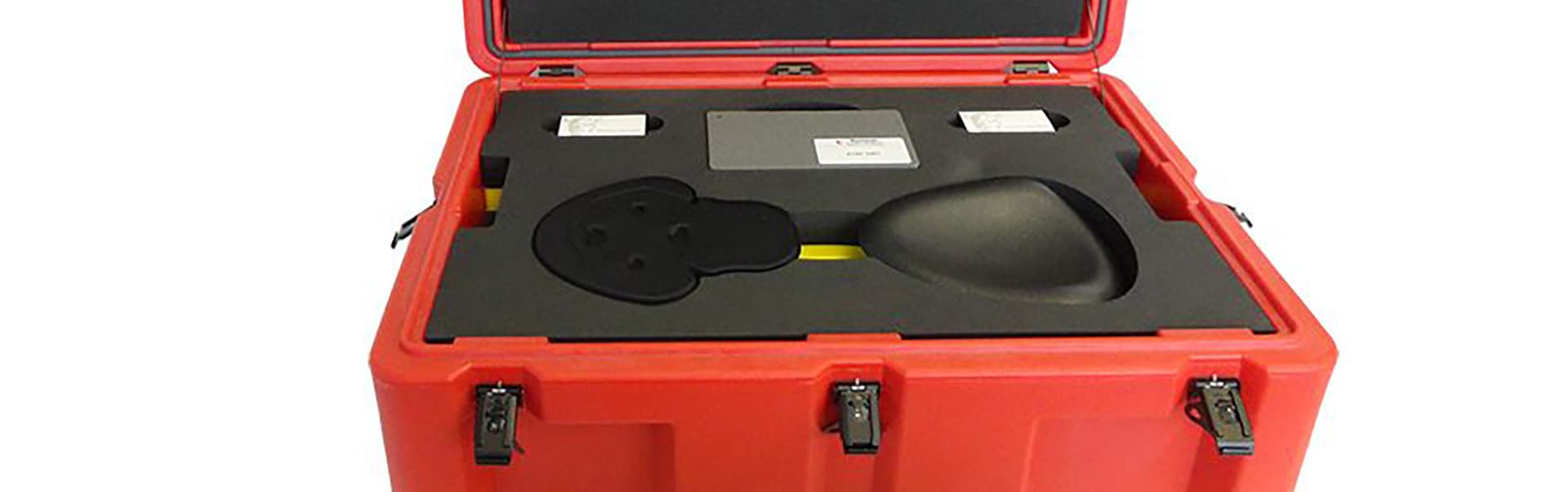
What’s Your Concept?
Foam fabrication solutions usually start with your concept. Is this case insert protecting a telescope or a set of tools? Will soft foam or a more rigid foam be the right approach? These are great questions when you sit down with a foam design expert.
Problem-solving through the conceptual phase is much easier when things like budget, adaptation from previous or existing designs and protection requirements are squared away.
Also, check to see if the case insert manufacturer you’re working with can utilize features like 3D modeling or CAD/CAM equipment to help create a realistic image of what you want your insert to look and feel like.
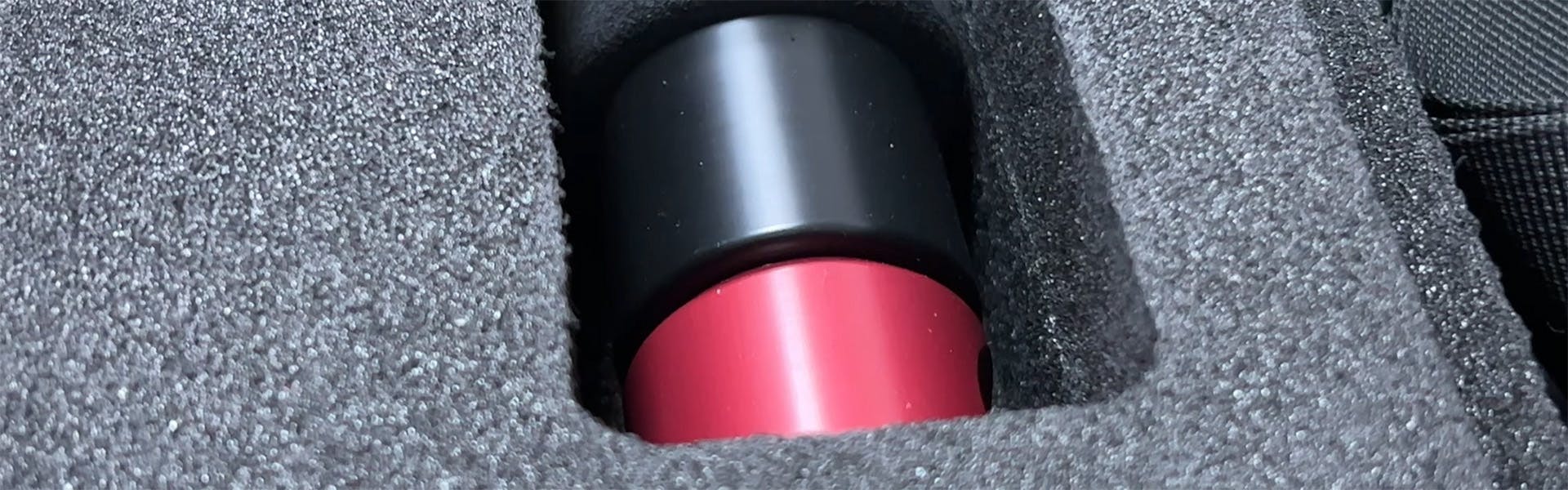
Determining Case Size
Understanding the concept and determining the suitable foam for the job are the first stepping stones of a custom case insert project. This gives an excellent overall picture of what the case insert will look like.
Now it's time to get down to the nitty-gritty, though. The size of a custom case insert depends primarily on the specific items to be stored or transported. A telescope will be different from a laptop. A microphone will have a different shape than a set of tools.
It's essential to consider the contents' precise measurements, weight, and distinctive characteristics so an appropriate size insert can be drafted for the case.
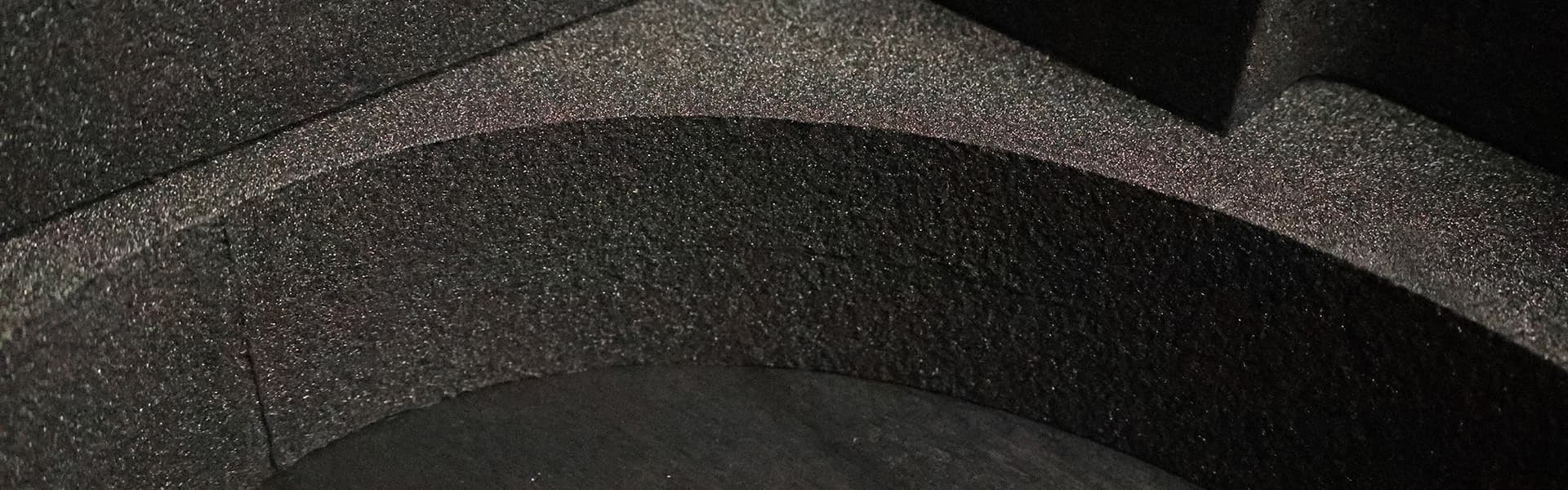
Figuring Out the Foam That Truly Fits!
Figuring out the concept and the initial design is excellent, but now it’s time to get to the real meat and potatoes of a custom case insert: the foam.
“Aren’t all foams the same?” you may ask, but this isn’t a cheesy infomercial, and the answer is, “Of course not!”
It would be exhausting to type out just how many different types of foam are available to the bulk of foam fabricators. It’s not even possible to list them all without it getting too much:
Cross-linked Polyethylene Foam (XLPE)
Zotefoams
Evazote
Plastazote
Extruded Polyethylene Foams
Polyurethane Foam
Reticulated Polyurethane Foam
Polyethylene (EPE) Foam
Expanded Polypropylene (EPP)
You get the picture.
This is why it’s imperative to work with your foam manufacturer to list your requirements and they’ll do the heavy lifting of finding the proper foam for you. It’s understandable to consider the application of each protective foam solution, but finding the right one for your project can usually be found by answering the following criteria…
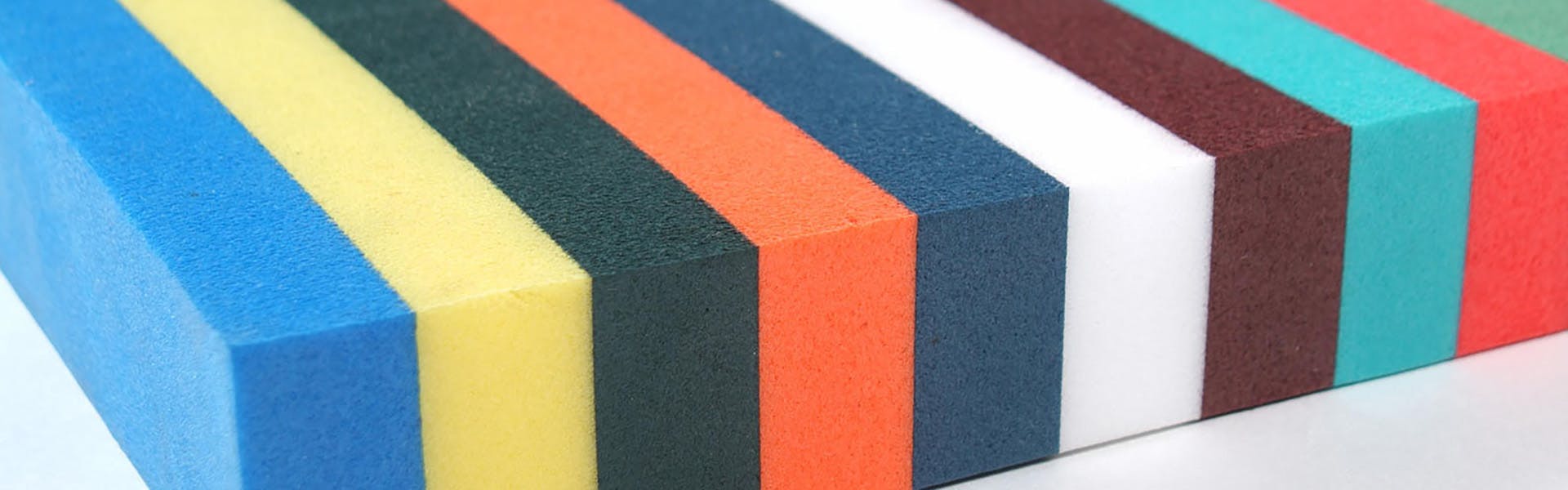
The Fab-Four Foam Criteria
Density: The density is a simple measurement of weight per unit of volume, usually done in pounds per cubic foot (PCF) or just pounds per foot. Density can range from around 1 lbs/ft up to 12 lbs/ft. Higher densities are also available.
A higher-density foam means it can handle a higher weight applied to it. A high-density foam will also tend to feel more firm. On the other hand, low-density foams will feel softer but might not withstand excessive pressure or weight
Rigidity: You mustn’t confuse rigidity with density, but they go hand-in-hand. Rigid foams include polyurethanes with a solid, “rigid” structure, while flexible polyurethanes have a soft and elastic structure.
Depending on how stiff you wish the foam to be can help narrow down which foam types will work best for you. Soft comfort foams are best for sports and leisure products, while more rigid ones are better for outdoor recreation and construction.
Unique Properties: This primarily comes down to preference. Foam color or design features like your company logo being cut into the foam. This is where you maximize personality over functionality. What statement do you want to send with your case insert?
Different foam properties can also include hypoallergenic foams for patient-to-patient contact in the medical industry or even marine-grade foams that meet ‘SOLAS’ approval for contact with water. Fire resistance ratings and shock dissipation capabilities are your case insert foam features.
Sustainability: Sustainable business practices are becoming more and more critical. Manufacturers who value preserving and positively impacting our environment bleed into things like the foam and manufacturing processes they use.
Tools and Machines: How Does It Take Shape?
Once you’ve selected the foam type and the design, it’s time to make the case insert take shape. Like a chef with their knives, foam manufacturers have many tools to cut the case insert to take form.
These tools can include the following:
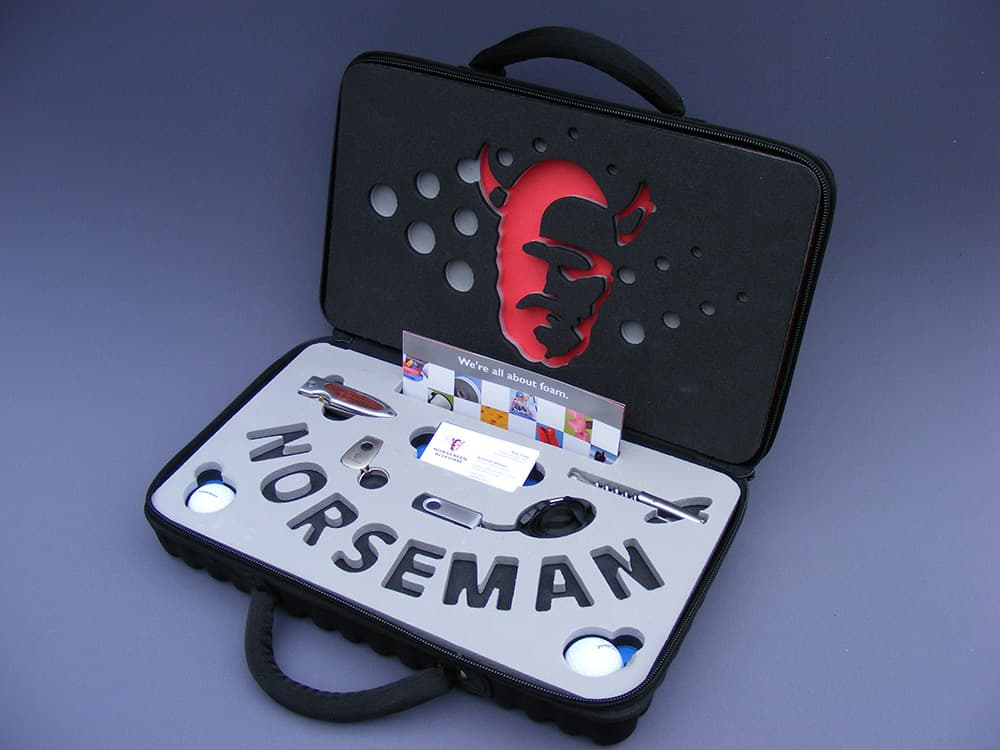
CNC Machines: CNC stands for Computer Numerical Control. These are computer-controlled cutting machines with mounted routers as a spindle that can be programmed to cut at different patterns and depths. These can be standard routers, water-jet CNCs that use high-pressure water, or hot wire CNCs that use a wire strand that heats up to cut through foams.
These machines are widespread for many foam manufacturers as they work as a panel saw, spindle molder and a boring machine in one. They can also cut joinery for any interlocking pieces.
Die Cutting: Die cutting uses a metal die or mold to shear through low-strength materials like foam. This process can be known as “clicking” or “dinking,” depending on the die used. This can be done on a flatbed or rotary press. These are standard processes for printing but can be used to imprint patterns or colors onto the foam of a case insert.
Splitting: Splitting machines efficiently shave raw materials in sheets to any required thickness. A horizontal steel blade is used to shave the foam sheet into two separate pieces. This helps create a uniform cut to keep the thickness consistent across the piece of foam. The resulting sheet or block can then be sent to die-cutting or CNC machines for further processing.
Lamination: This process is when two different foam pieces are fused or if a foam piece is fused to a separate fabric or plastic piece. An adhesive is applied in this process and must be highly flexible to accommodate different foam types. This process can create two other foams for a two-tone texture feel. Lamination can also build strength in the foam insert, making manufacturing processes more efficient.
Thermoforming/Compression Molding: Thermoforming is a process that involves heating a plastic or foam sheet to a pliable temperature that will then form into a specific shape or mold and be trimmed. A small tabletop or more extensive industrial foam machine can be used.
Compression molding is when the material is preheated in an open mold cavity and then closed with a top piece. The pressure of the compression and the heat will mold the foam into a specific shape. These are high-volume, high-pressure methods used primarily for composite thermoplastics.
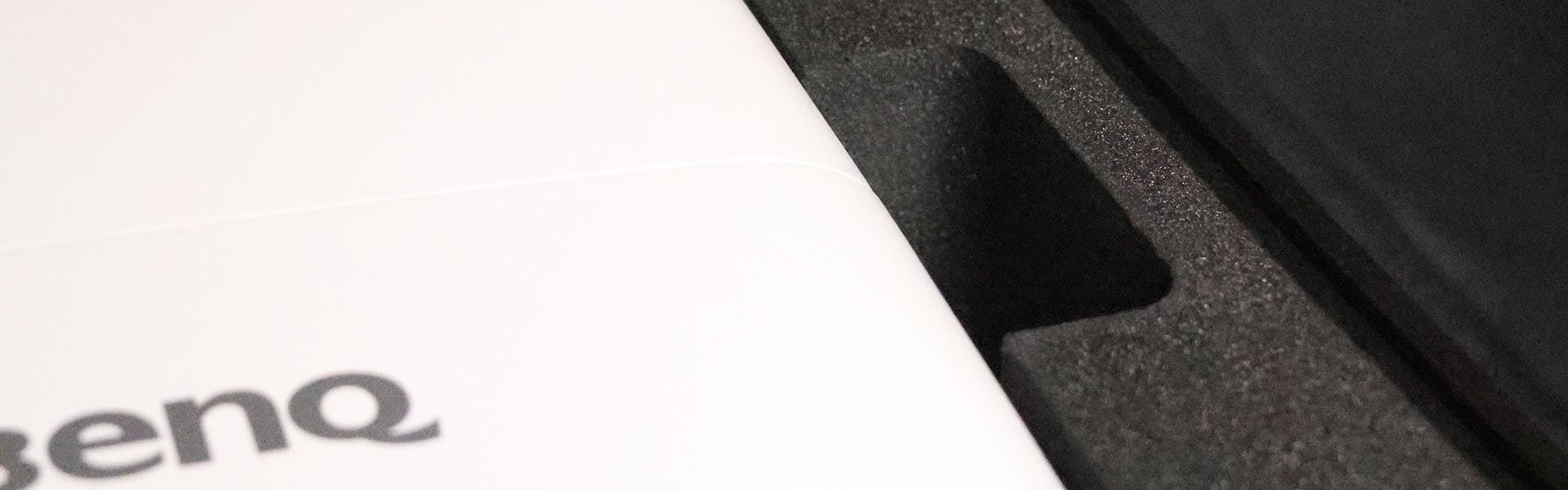
Final Consultation and Placing The Order
Working with your foam fabrication manufacturer is always essential. The concept and design stages are the build-up to finally jumping in and making the commitment to place your order.
Once the materials and features are locked in it's finally time to place an order. Clear communication and adherence to agreed-upon terms are crucial to discussing production timelines, quantities and pricing.
This is the last but arguably most important step in designing your custom foam insert. It's the so-called point of no return, but it's also the time to double-check and triple-check your project's capacities to ensure it's designed to your ultimate specification.
After this step, the prototype stage can begin!
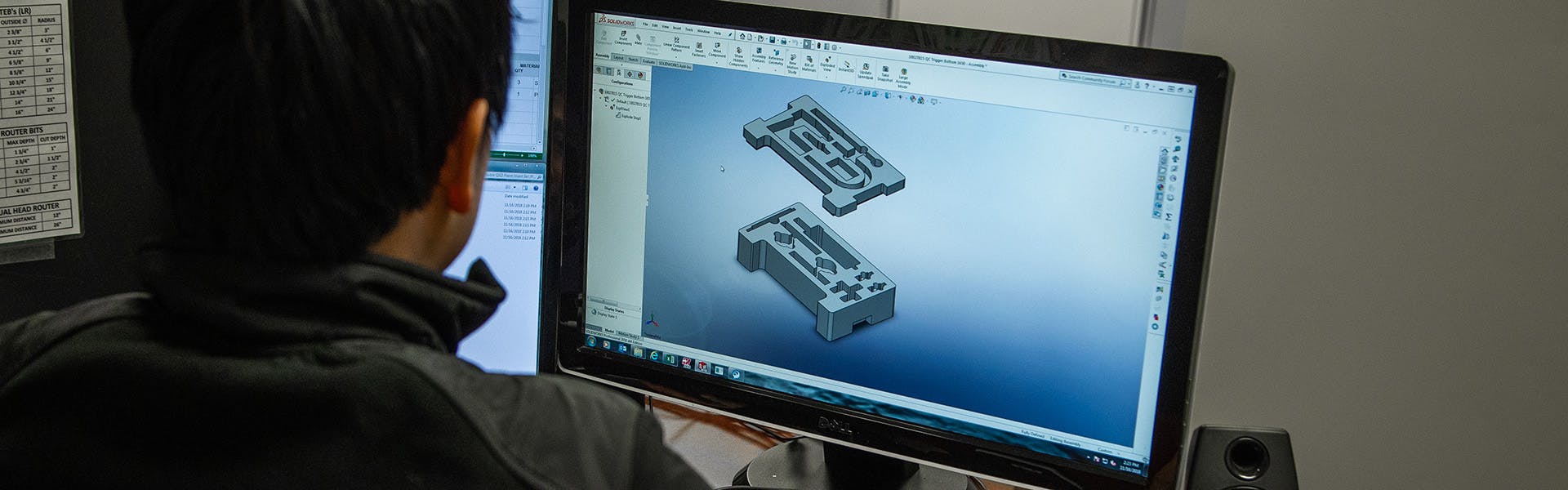
Let’s Make a Prototype
Once the concept and design have been discussed and squared away, we can now move into designing the prototype for your case insert. Up to this point, the case insert has only sounded good in theory, now it’s time to see it in practice.
Most manufacturers utilize CAD/CAM equipment and capabilities to produce 3-dimensional prototypes to validate and test in the prototype phase. Seeing is believing, and that’s why this stage is crucial for you to feel what a finished product will look like.
Prototypes take your conceptual ideas from the design table and create a solid model rendering or 3D sketch of your innovation. Proof-of-concept, 3D printing services, molded parts, or even functional prototypes can be designed to give you the whole idea of your project before it goes to full production.
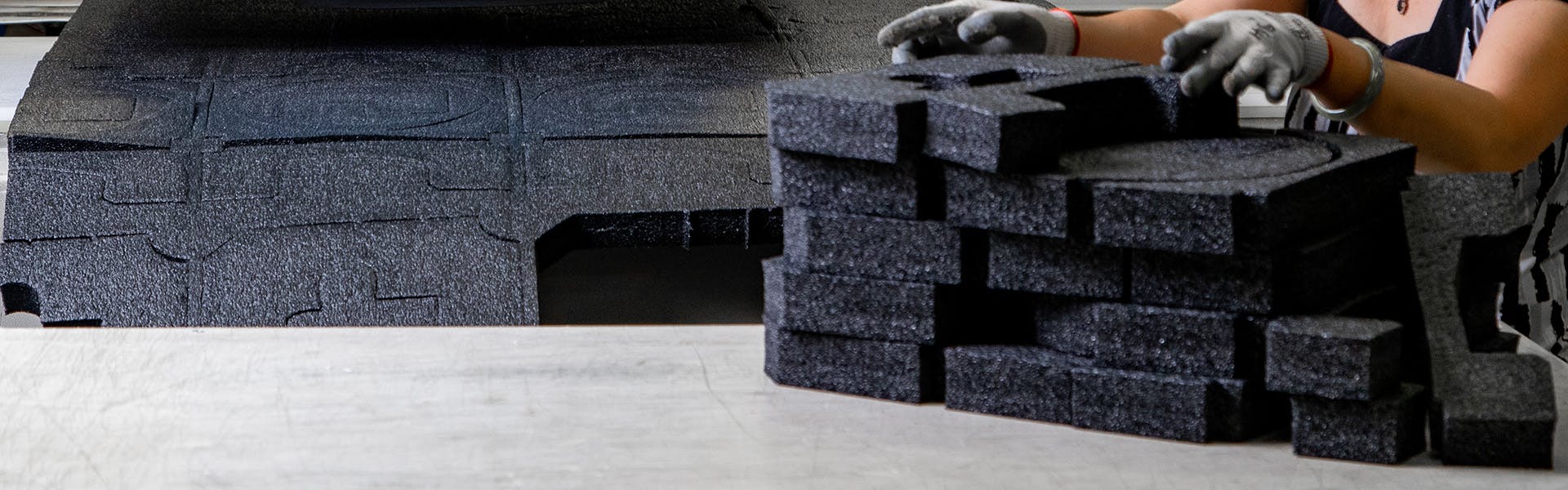
Other Features
When solidifying your concept and designing the prototype, you must consider all the little nooks and crannies that maximize customization for your insert. Everything from how the product will fit within the case to the shape of the case and how that may affect your insert’s layout.
Let’s take a quick look at a few of these other features to consider when designing.
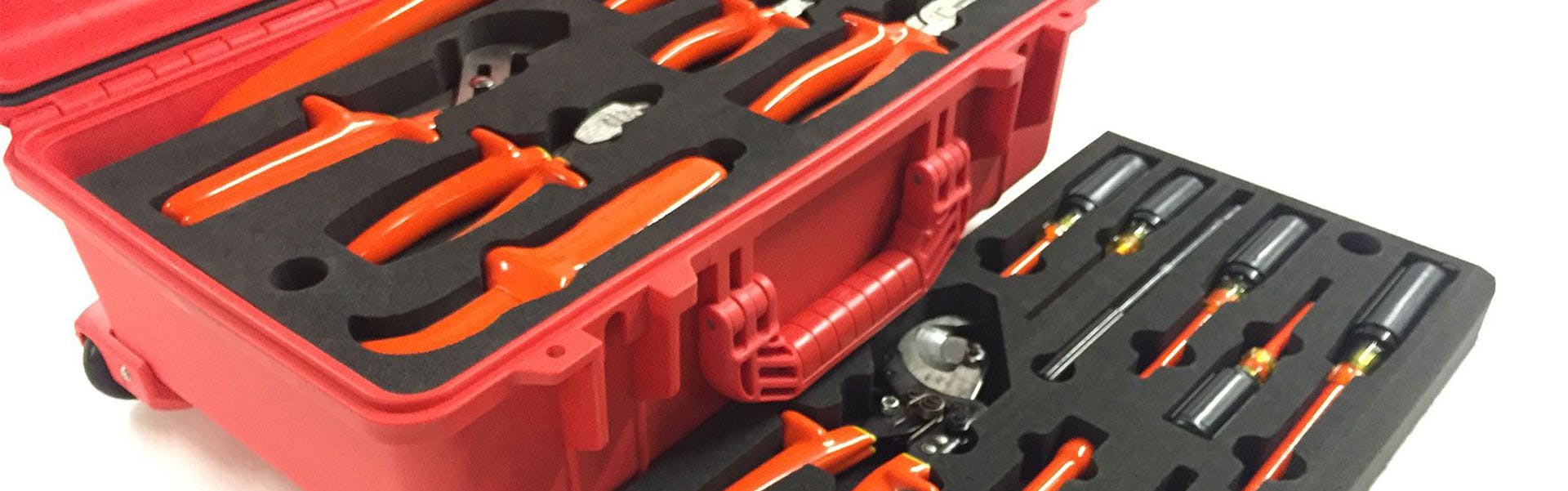
Understanding the Case Type
Let’s say we’re going with a hard-shell case for our insert. These cases protect against external impacts, moisture and several other environmental factors. These cases are ideal for delicate or valuable equipment; a higher foam density and low rigidity might help bolster the protection the insert offers to the case.
Conversely, soft-shell containers have a priority of being lightweight and flexible. Products in them require less rugged production and a higher rigidity foam might be used on the insert for more container shape.
Other options include the following:
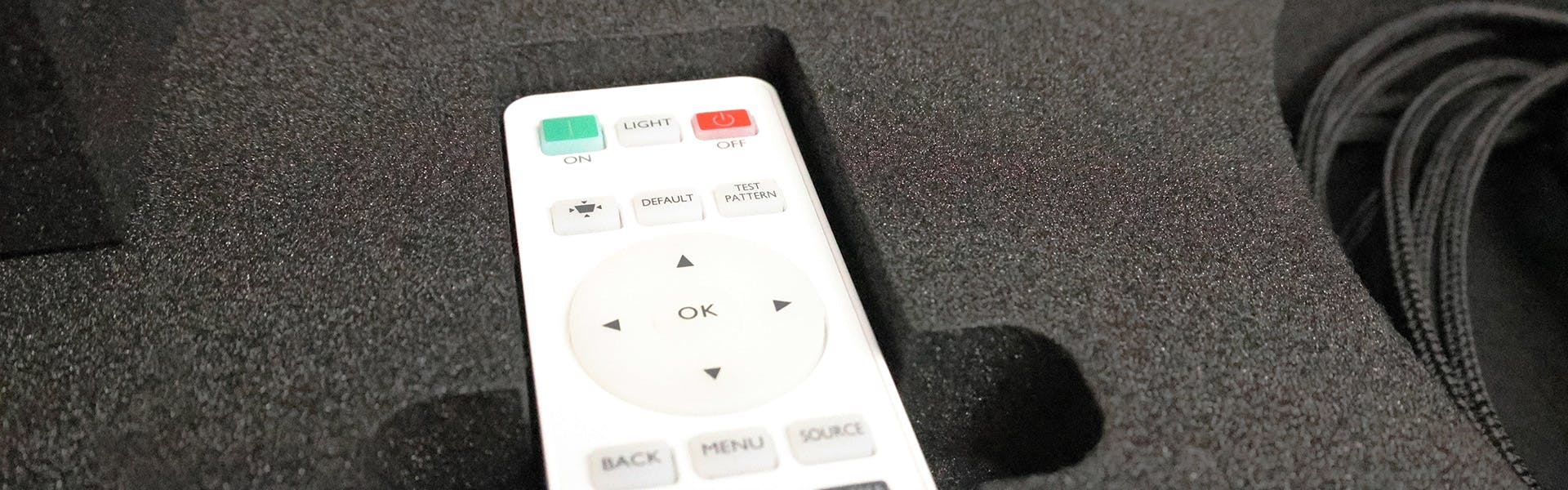
Case Accessories or Features
Your custom case insert may have to be adjusted for different accessories or features on the case. Things like wheels, divider pockets, retractable handles, straps and even zipper placement of the case must be considered when designing your insert.
Precision-cut foam from the manufacturer for the case inserts is one of the most common features when designing it for a custom-carrying case. The insert can be cut to fit around any of these case features and protect the belongings inside.
Consider Branding Elements On Your Insert
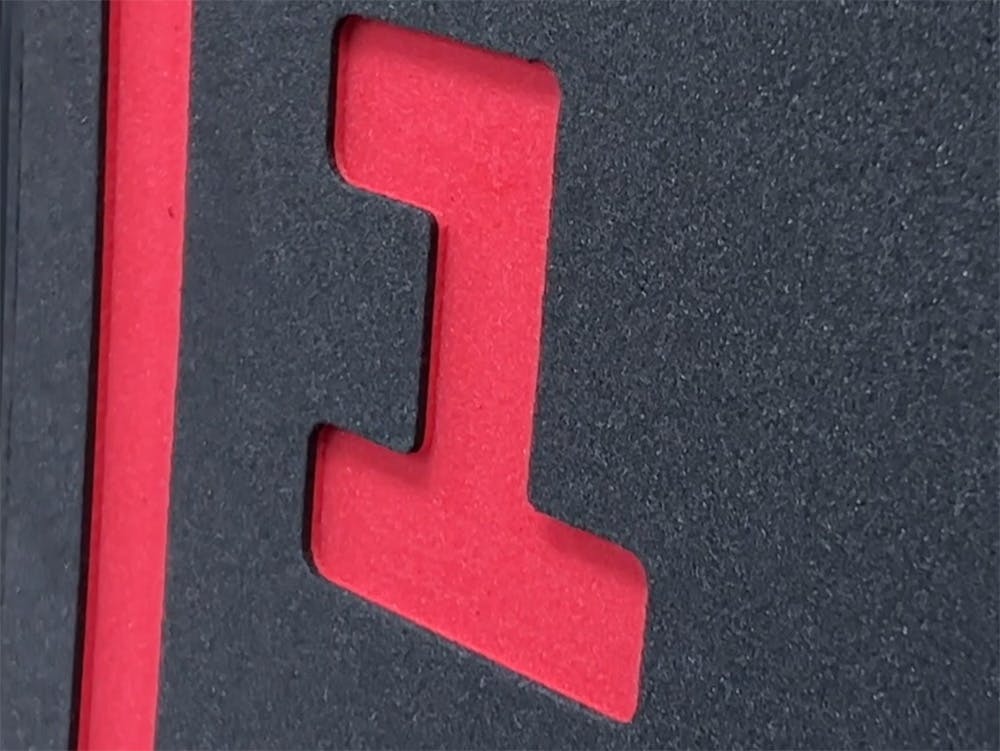
Why would you go through the customization process without wanting to leave your mark? A case should be a reflection of you, the user. When that case opens, having foams to your company's color scheme, with the company or your logo engraved into the foam, are all signature touches that can be done in the planning process of your insert.
Branding is essential in the modern landscape to stand out. It creates a distinct identity that leaves an impression on all who see it. This is especially true if your insert will be used in a promotional context. It's working with the manufacturer to incorporate the logo, colors, etc., to accompany the case's functionality.
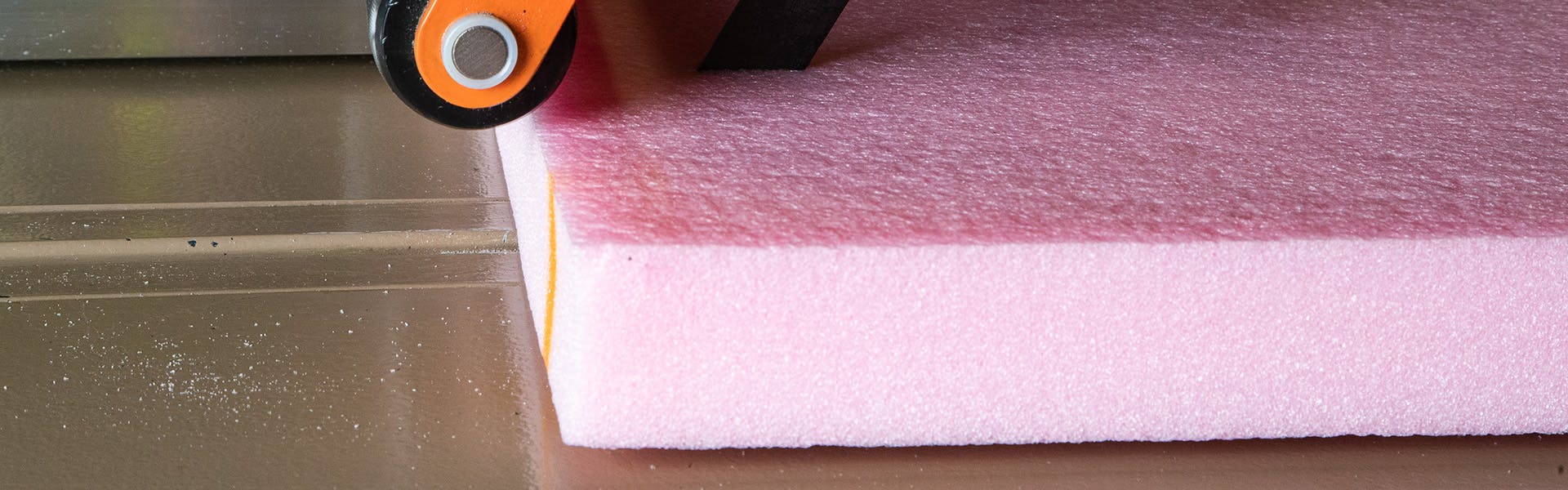
Summary - Don’t ‘Foam’ It In
Custom case inserts give you complete creative control if you want maximum customization and that next-level edge for your equipment and branding capabilities.
You wouldn’t want to trust something requiring a precise touch to just anyone. Through it all, the custom case manufacturer you work with has to be your dependable partner.
Working through high-quality foam selections to create a custom solution can become a labyrinth of decisions, so the process mustn’t overwhelm you. Running ideas of the rep you work with will help them generate enough of a workflow to narrow down the options and get you what you need for the project.
Doing your due diligence is imperative on these types of projects. Once that design is solidified and the manufacturer produces a functional prototype to your satisfaction, the only thing left is to make it a reality.